-
Un article fort intéressant sur les charbons
Le remplacement d'un jeu de balais de charbon usé ou dégradé est une opération des plus simples et des plus faciles à réussir... à condition de disposer d'éléments de rechange exactement semblables, en dimensions et qualité à ceux qui sont détériorés. Dans le cas contraire, on peut être tenté, au lieu de faire attendre le client pendant la durée d'un réapprovisionnement, d'ajuster de nouveaux balais improvisés, découpés dans d'autres types de charbons de plus forte taille et de qualité inconnue.
Nous allons examiner pourquoi une telle manière d'opérer qui risque d'entraîner les incidents les plus graves, ne doit être effectuée de cette manière qu'en cas de dépannage urgent et temporaire et doit obligatoirement être suivie, à courte échéance, d'une remise en état parfaite, avec des pièces d'origine et selon les règles, de l'art.
Rappel de principes
 Fig. 1. - Schéma de principe d'une dynamo A à K Circuit d'une section d'enroulement induit. - P, Q Lames de collecteur. F1, F, Balais. N, S Pièces polaires des inducteurs. - X Y Axe de rotation du rotor.
Rappelons sommairement le principe de la dynamo. Un enroulement "induit", représenté schématiquement sur la figure 1 par une double spire A B C D E F G H J K peut tourner autour d'un axe X Y entre les "inducteurs" électromagnétiques N et S et dans le champ magnétique développé par ceux-ci. La force électromotrice demandée à la dynamo est proportionnelle au produit de la self-induction de l'enroulement de la bobine par la variation du flux magnétique qui en traverse les spires. Ce flux est maximum lorsque les spires considérées se trouvent dans la position indiquée sur la figure (c'est-à-dire, ici, horizontalement). Il est minimum et même nul quand les spires sont placées parallèlement au champ magnétique (ici verticalement).
A vitesse de rotation constante nous avons affaire à un phénomène périodique sensiblement sinusoïdal. Dans tous les phénomènes sinusoïdaux, la vitesse de variation est nulle à l'instant où la valeur absolue est maximum et elle est maximum au moment où cette valeur passe par zéro. Dans notre exemple, il est facile de se rendre compte qu'au voisinage de la position horizontale figurée, un petit changement de la position angulaire de la spire n'entraîne qu'une variation négligeable du flux magnétique qui la traverse tandis que lorsque la spire passe par le plan vertical parallèle au champ magnétique, il suffit d'un très faible changement de sa position angulaire pour que le sens du champ magnétique qui traverse la spire se trouve inversé, ce qui représente la plus grande variation qui puisse lui arriver.
Ainsi donc, le flux qui traverse la spire est allé en diminuant depuis le maximum correspondant à la position indiquée par la figure, jusqu'au passage à la verticale où se produira l'inversion du flux à l'instant où il devient nul. A la suite de cette inversion, le flux ira, au contraire, en croissant mais, du fait du renversement de la spire et de l'inversion du sens du flux qui en résulte, la variation du flux, vu de la bobine, se retrouvera de même signe durant le deuxième quart de tour que pendant le premier.
- Nécessité de la commutation
Au contraire, au moment où la spire repassera par la position horizontale (celle de la figure) le flux qui la traverse ne pourra plus augmenter puisqu'il est égal à la totalité du flux qui passe dans l'induit. Il va donc commencer à diminuer, mais très lentement puisqu'un changement appréciable de position angulaire de la bobine ne produit qu'une variation négligeable du flux qu'elle embrasse dans cette région de son mouvement (ainsi que nous l'avons signalé pour la sinusoïde, la grandeur du flux étant maximum, sa variation est nulle).
Mais en même temps que cette variation s'annule, nous voyons qu'elle-même change de signe ainsi que la force électromotrice qui en résulte. C'est donc dans cette position du flux maximum qu'il y aura lieu de faire intervenir une commutation si l'on veut que le courant résultant, dans le circuit extérieur, des forces électromotrices de la bobine, reste de même sens que pendant le demi-tour précédent, ce qui est indispensable à la production, par la machine, d'un courant continu (il a d'ailleurs été démontré qu'il est théoriquement impossible d'extraire du courant continu d'une machine tournante sans passer par un contact glissant). Dans le cas de notre figure, la commutation consistera, simplement en une inversion des connexions des extrémités de l'enroulement induit avec les conducteurs de sortie du courant induit qui sera obtenue à l'aide d'un collecteur à deux coquilles hémicylindriques, P et Q. tournant solidairement du bobinage induit, et dont les surfaces conductrices pourront glisser sous les balais F 1 et F 2 reliés au circuit d'utilisation.
Remarquons, et insistons encore car ceci est très important, que c'est à l'instant où le flux embrassé par la bobine passe par un maximum que doit être opérée la commutation. Alors, la variation du flux passe par la valeur zéro ainsi que la force électromotrice qui résulte de cette variation. Cette coïncidence est la circonstance la plus heureuse qui puisse se présenter pour la réussite d'une bonne commutation. Toutefois nous verrons qu'en pratique elle ne peut pas être obtenue et conservée en toutes circonstances avec une précision suffisante pour être utilisée sans faire intervenir les artifices d'une technique très élaborée dont nous allons essayer de présenter la justification.
Principalement pour des raisons de régularité et de continuité de débit les enroulements induits des dynamos sont généralement constitués, comme bien connu des spécialistes, par de multiples bobinages connectés en série ou en, série-parallèle avec leurs points de jonction reliés respectivement aux multiples lames d'un collecteur.
 Fig. 2. - Représentation schématique, développée en longueur, du passage des lames du collecteur C : 1, 2, 3, 4... sous la face d'appui du balai B.
Sur la figure 2, nous avons schématisé linéairement les lames 1, 2, 3, 4 d'un collecteur C qui défilent successivement sous la surface de contact d'un balai B, chacune de ces lames étant connectée au point de jonction, en série, d'autant de sections de bobines représentées au-dessous.
- Analyse du problème
Supposons d'abord que la longueur de la portée du balai, selon la surface
circonférentielle du collecteur, soit égale à la largeur des lames (nous négligerons ici l'épaisseur des cloisons isolantes) et que l'intensité du courant passant par le balai B ait tendance à se répartir, entre les deux lames consécutives 2 et 3 couvertes par le balai, proportionnellement aux surfaces de contact avec ces deux lames.
 Fig. 3. - Graphique représentant l'intensité du courant, portée en ordonnées de 0 à 15 ampères, en fonction de la fraction utilisée du balai, fraction porté&;e en abscisse de 0 à 10
Pour bien analyser le phénomène représentons, (fig. 3) horizontalement, en abscisses, la longueur de portée du balai, grande échelle, que nous graduerons de 0 à 10 du point o au point D. Nous porterons verticalement, en ordonnées, la valeur du courant débité par la lame 2 (fig. 2) pendant qu'elle glisse sous le balai B en supposant que le débit de celui-ci se maintient à la valeur constante de 15 ampères, par exemple. Prenons pour section du balai la valeur d'un centimètre carré ; chacune des divisions de l'abscisse de 0 à 10 représentera un dixième de centimètre carré. A l'instant où la ligne de séparation entre les lames 2 et 3 abordera l'entrée du balai B. la lame 2 sera entièrement couverte par le balai et la densité de courant à la surface de contact sera de 15 ampères par centimètre carré. Au fur et à mesure que la ligne de séparation entre les lames 2 et 3 avancera sous le balai en franchissant les divisions de 1 à 10 de notre graphique : le courant débité par la lame 2 diminuera dans la même proportion que la surface couverte sur cette lame par le balai et pourra être représenté par la ligne droite 15-A-B-C-D, c'est-à-dire à densité de courant constante. En effet, en tout point tel que A de cette droite, l'intensité correspondante (6 ampères) devra passer par la surface restante, de 6 à 10, soit 4/10 de centimètre carré, soit 6 0,4 = 15 A/cm2.
En même temps, le complément du courant de 15 ampères ira en augmentant dans la lame 3.
Mais la réalité est loin d'être aussi simple car alors intervient la self-induction de la section d'enroulement couverte par le balai. Remarquons ici qu'il est impossible de supprimer cette self-induction sans stériliser la machine puisque la force électromotrice de celle-ci, comme nous l'avons vu au début de cet article, est proportionnelle au produit de cette self-induction par la variation du flux.
Or, l'effet de la self-induction est de retarder les variations du courant dans les spires qu'il parcourt.
Dans un enroulement normal, le retard ainsi introduit est extrêmement petit, de l'ordre de quelques dix-millièmes de seconde, mais nous allons voir qu'il peut entraîner des conséquences très importants. A la vitesse de rotation de 5.000 tours par minute, et pour un collecteur à 13 lames, la durée de passage d'une lame sous le balai est inférieure à un millième de seconde. En admettant un retard de trois dix-millièmes de seconde dû à la self de la section 2-3 de l'induit, ce qui est une valeur normale, le graphique de notre figure 3 nous montre, par exemple, que lorsque la ligne de séparation des lames aura atteint le point 6 qui correspondrait à une intensité A de 6 ampères s'il n'y avait pas de self, il faudra encore attendre trois dix-millièmes de seconde pour que l'intensité soit descendue à la même valeur et pendant lesquels la ligne de séparation aura parcouru la distance de 6 à 9. Le point correspondant à l'intensité de 6 ampères se trouvera reporté de A en F et la courbe représentative de l'intensité débitée par la lame 2 en fonction de sa course sous le balai ne sera plus la droite 15-A mais aura l'allure 15-EF.
Aux 6/10 du balai, il ne restera plus que 4/10 de section utilisée tandis que l'intensité, primitivement de 6 ampères au point A sera maintenant portée aux 10 ampères du point E. La densité de courant sera ainsi devenue égale à 10/0,4 = 25 ampères par centimètre carré. De même au point F correspondant à 9/10 de course sous le balai, la surface utilisée n'est plus que d'un dixième de centimètre carré tandis que l'intensité, au lieu de 1,5 ampères au point B, est encore de 6 ampères ; la densité atteint alors 60 A/cm2. Lorsqu'il ne reste que 5 % de surface utilisée, l'intensité de 0,75 A du point C est devenue 5 A au point G et la densité atteint la valeur de 100 ampères par centimètre carré, qui est énorme et inadmissible pour un frotteur glissant.
Mais là où tout cela devient tragique c'est qu'il faut bien que le courant devienne nul lorsque la ligne de séparation atteint le point 10 et que la lame sort de sous le balai. Comme la diminution d'intensité est toujours en retard, l'allure de la courbe devient de plus en plus verticale ce qui signifie que la densité de courant tend, à mesure qu'on approche du point D, à devenir infiniment grande.
On conçoit que le bord extrême de sortie du balai soumis à ce régime puisse atteindre une température localement très élevée et que la coupure du courant au même endroit sous une densité de courant énorme, transforme les particules de charbon de l'arête en microscopiques lampes à arc, d'où, comme conséquence immédiate, combustion et désagrégation du charbon et brûlage des lames du collecteur.
- Premiers remèdes
La théorie et le calcul nous enseignent et l'expérience vérifie qu'en appliquant une tension continue auxiliaire constante de quelques volts jans le sens convenable entre le balai et la lame du collecteur, on peut déformer la courbe E F G D de notre graphique, la rapprocher, et même la faire passer au-dessous, de la droite AD, auquel cas il ne faudrait pas exagérer car on provoquerait une arrivée au point D par le dessous avec une pente de sens inverse qui aurait le même inconvénient, changé seulement de signe, d'une excessive densité de courant à l'arête de sortie du balai. Une tension auxiliaire judicieusement dosée permet de rapprocher la courbe ED de la droite AD, sans toutefois la rectifier complètement, mais en atténuant beaucoup la pente finale, ce qui est l'essentiel.
Dans les anciennes machines où l'on utilisait des balais métalliques, on obtenait bette tension auxiliaire en décalant l'alignement diamétral des balais par rapport à la ligne neutre du champ magnétique inducteur. L'inconvénient grave de ce procédé était de favoriser la déformation du champ inducteur par les ampères-tours des enroulements induits, déformation bien connue des constructeurs de machines tournantes sous le nom de "réaction d'induit" et contre laquelle ils s'efforcent de lutter car sa variation, en fonction de l'intensité, s'ajoute défavorablement aux autres courses de la chute de tension totale de la machine avec la charge.
- La chute de tension de contact
C'est ici que commencent à intervenir heureusement les propriétés particulières du graphite qui entre dans la constitution des balais, propriétés qui placent cette forme de carbone dans une classe intermédiaire entre les bons conducteurs (métaux) et les "semi-conducteurs" dont les caractéristiques très spéciales ont été étudiées, recherchées et améliorées en vue de leur utilisation dans le domaine encore nouveau des redresseurs diodes et des transistors. A la surface de contact entre le graphite du balai et le cuivre du collecteur, l'intensité du courant provoque l'apparition d'une chute de tension de contact qui n'a rien de commun avec la chute ohmique car elle varie peu avec l'intensité. Par un choix convenable des matières entrant dans la composition du balai et de leur dosage, on arrive à obtenir que cette chute de tension au contact présente une valeur (de l'ordre d'un volt et demi) correspondant à celle qui est précisément favorable à l'amélioration de la courbe de notre graphique.
Le décalage des balais, autrefois assez fort avec les balais métalliques, obligeait à un réglage incessant en fonction des variations de la charge. Les balais de charbon, en réduisant ce décalage à une très faible valeur, souvent nulle, nous ont délivré de ce souci constant de retouche du réglage.
Pour une même qualité de charbon, la chute de tension de contact n'est d'ailleurs pas égale pour les deux sens de passage de courant. C'est pourquoi les machines dynamos très spéciales à très basse tension (quelquefois 2 volts) destinées à l'industrie électrochimique sont parfois équipées de deux qualités différentes de balais pour la sortie et l'entrée du courant au collecteur.
- La résistance ohmique
La self-induction des enroulements de l'induit, en outre de l'inconvénient que nous venons d'étudier avec ses remèdes, vient encore nous jouer de mauvais tours sous la forme de "l'extra-courant" dû à la variation brusque de l'intensité dans la section d'enroulement considérée (il s'agit ici de la variation de l'intensité totale dans les spires et non plus de la densité de courant). A l'instant où les lames se trouvent court-circuitée par le balai, le courant de court-circuit tend à prendre une intensité qui n'est limitée que par la très faible résistance de la section et la rupture de cette intensité occasionne une surtension qui vient perturber les résultats de nos efforts. C'est ce qu'on appelle la "tension de réactance" de la section.
C'est alors qu'intervient, heureusement encore, une seconde propriété de notre balai de charbon, sa résistance ohmique, laquelle évite le court-circuit franc de la section, limitant ainsi l'intensité et la surtension d'extra-courant.
En contrepartie de cet avantage, la résistance ohmique du balai présente l'inconvénient d'une chute de tension supplémentaire, proportionnelle, celle-là, à l'intensité, dont l'inconvénient le plus grave n'est pas la perte de rendement qui lui correspond, mais un échauffement éventuellement exagéré du collecteur et des isolants des porte-balais déjà exposés à la chaleur due au frottement.
Encore une fois c'est par une solution de compromis qu'on devra résoudre pratiquement le problème par un choix du dosage des éléments constitutifs des balais.
D'après ce qui précède, on voit qu'à l'endroit exact où se produit la séparation de la lame de collecteur et du balai et à l'instant précis de cette rupture, la tension doit être très voisine de zéro. Or cette tension est la résultante de la superposition de plusieurs forces électromotrices dont les trois principales sont : 1° la chute de tension au contact qui dépend de la composition chimique du balai ; 2° la tension de réactance (self-induction de la section) qui dépend de l'intensité de court-circuit entre deux lames et, par conséquent de la résistivité, donc de la texture du balai ; 3° la tension de réaction d'induit correspondant au meilleur réglage du décalage angulaire, lequel est dépendant des deux forces électromatrices précédentes.
Comme la réaction d'induit et la tension de réactance peuvent varier beaucoup d'un type de machine à l'autre, principalement selon le profil des faces polaires, le degré de saturation magnétique des cornes polaires et la forme de la denture d'induit, on conçoit que le choix de la qualité du charbon qui assure la plus longue durée de fonctionnement correct d'un collecteur ne puisse être que le résultat d'une étude et d'une mise au point prolongée au laboratoire et que ce n'est que par un coup de chance que l'estimation au jugé d'une qualité de remplacement peut permettre un dépannage acceptable.
Après cet exposé, nécessairement assez sommaire, des principaux problèmes posés par la commutation et de quelques procédés qui permettent de les résoudre, au moins partiellement, voyons maintenant les fabrications que le marché nous propose, quelles sont les propriétés mécaniques et électriques des produits résultant de ces fabrications et la répercussion de ces propriétés sur les conditions et les résultats de leur utilisation.
- Propriétés physiques des balais de charbon
Densité. — A partir des différentes qualités de carbone dont les densités s'échelonnent entre 1,4 et 2,2 on obtient, pour les agglomérés cuits, des densités voisines de 1,8, un peu plus élevées après graphitisation au four électrique.
L'introduction, dans le mélange, de métaux de densités comprises entre 8 et 9 font naturellement monter cette valeur. Par exemple, des balais contenant la moitié de leur poids de cuivre ont une densité de 3 environ. Pour une proportion de trois-quarts de cuivre contre un quart de carbone, la densité monte vers 4,5. Des mélanges très riches en bronze, ne contenant plus que 7 à 8 % de carbone atteignent une densité de 5,9.
Les hautes densités ne sont pas recherchées pour elles-mêmes mais sont inséparables des hautes conductibilités électriques. Elles n'ont qu'un léger inconvénient, celui d'exiger, dans les applications aux machines soumises à de très fortes trépidations, une force des ressorts de pression suffisante pour éviter le décollement entre les balais et le collecteur.
Porosité. - Contrairement à la porosité des charbons de cornue qui était de l'ordre des dixièmes, celle des agglomérés n'atteint que quelques centièmes. Comme la porosité est généralement accompagnée de fragilité, on cherche à la réduire le plus possible par des soins apportés lors de la compression et en réduisant au minimum la proportion d'agglomérants susceptibles de disparaître à la cuisson. Dans un seul cas, de plus en plus rare, la porosité peut être utile lorsqu'on recherche la résistivité ohmique élevée exigée par d'anciennes machines présentant de fortes surtensions entre les lames du collecteur.
Dureté. - La dureté d'un mélange aggloméré ne se définit pas aussi aisément que celle d'un alliage métallique car on, ne peut la mesurer par des méthodes telles que celle de la bille de Brunel, où l'on opère par écrasement local, celui-ci ayant précisément pour effet d'augmenter la dureté par une sorte d'écrouissage ou de la diminuer par effritement. On cherche à la déterminer par un procédé de rebondissement d'un percuteur (sclérométrie) et à la caractériser par un "indice" numérique qui peut varier du simple ou triple, entre des valeurs de l'ordre de celles que l'on rencontre dans les calcaires naturels.
Abrasivité. - L'exemple typique du "brunissage" des métaux à l'aide d'outil (brunissoirs) en pierres précieuses, de l'agathe au saphir, montre que la notion d'abrasivité n'est pas synonyme de dureté ni nécessairement conséquence de celle-ci. L'abrasivité des balais, lorsqu'elle est excessive et entraîne une usure exagérée du collecteur, peut provenir d'impuretés des matières premières qui, pour cette raison, doivent être choisies et sélectionnées avec un grand soin en recherchant une très faible teneur en cendres. Un charbon peut présenter une haute dureté, qui le protège de l'usure, prendre un beau poli et se comporter finalement, vis-à-vis du collecteur, comme un brunissoir. Toutefois un balai très tendre et doué, à cause de cela, d'une légère plasticité, peut s'adapter à de légères déformations longitudinales du collecteur et corriger également une petite insuffisance d'ajustage. Une certaine plasticité est également une protection contre l'engrènement auquel peut être exposé un balai trop dur au contact d'un collecteur en mauvais état.
Résistance mécanique. - C est à la flexion que le balai est soumis à des efforts mécaniques menaçant de le briser. C'est aussi à la flexion qu'il est le plus facile de le soumettre aux épreuves de la résistance mécanique. Cette dernière s'exprime toutefois, en kilogrammes par centimètres carrés, par la traction par unité de section qu'il faut leur faire subir pour amener la rupture et cela pour deux raisons dont l'une est que la matière du balai est moins résistante à la traction qu'à la compression et l'autre parce qu'au cours de l'effet de flexion, c'est à partir de la surface latérale la plus tendue que s'amorce la rupture.
La résistance à la "contrainte" de rupture à la traction, de l'ordre de 70 kg/cm2 pour les balais les plus tendres peut s'élever, pour certains balais durs au bronze, jusque vers 1.500 kg/cm2.
Clivabilité. - Lors du moulage à la presse, la matière comprimée, sous l'action combinée de la poussée du piston et du frottement des parois latérales du moule, tend à se répartir en couches parallèles à la face d'appui du piston et à prendre une texture feuilletée (schisteuse, comme disent les minéralogistes) analogue à celle de l'ardoise et susceptible de provoquer des écaillements à l'arête de sortie du collecteur lorsque le sens du feuilletage n'est pas parallèle au mouvement.
Les perfectionnements de la technique de fabrication ont fait pratiquement disparaître cette imperfection, que l'on rencontre encore souvent dans des balais à base de graphites naturels, un peu anciens. C'est pourquoi il est indispensable de respecter le sens de présentation du balai devant le collecteur lorsqu'on improvise un balai de remplacement de dépannage en découpant celui-ci dans un ancien balai de dynamo ou de moteur d'atelier, de plus forte taille.
Résistivité. - Cette caractéristique, qu'il est inutile de définir ici puisque nos lecteurs sont spécialistes, peut différer dans de très fortes proportions d'un type de balai à l'autre. De quelques milliers aux dizaines de mille unités pour les balais composés uniquement de diverses qualités de carbone, elle peut descendre franchement au-dessous de mille microhms-centimètre dans les compositions richement métallisées. Nous avons vu, dans notre étude sommaire de la commutation, que ce n'est pas toujours le minimum de résistivité qui est le plus recherché. Dans les balais schisteux, elle peut présenter une valeur sensiblement plus élevée selon la mesure dans un sens de courant perpendiculaire au clivage.
La résistivité est d'autant moins grande que la composition est plus riche en métal. Une très forte teneur en cuivre, et par conséquent une forte conductibilité, conviennent aux machines débitant sous 6 volts. Une teneur moyenne satisfait une commutation sous 12 volts tandis qu'une dynamo donnant 24 volts exige une faible teneur de cuivre.
Les balais métallisés au bronze sont à la fois très conducteurs et assez durs ; ils sont particulièrement recommandés pour les démarreurs.
90 % des balais de dynamo dont du type graphitique tandis que 95 % des balais de démarreurs sont fortement métallisés (statistique portant sur 300 types de machines).
Pour concilier la résistivité nécessaire à la bonne commutation avec une faible perte ohmique le long du balai, de nombreux balais de dynamos sont recouverts, électrolytiquement, d'une couche très conductrice de cuivre rouge sur une grande partie de leur longueur. Naturellement, cette couche métallique ne doit pas approcher de trop près la surface frottante du balai, ce qui shunterait la résistivité transversale.
Pour annuler la résistivité de contact entre le corps du balai et la coulisse du porte-balai, un shunt en tresse de cuivre rouge est souvent établi, surtout pour les très basses tensions et fortes intensités. Ces shunts peuvent justifier une assez notable majoration du prix des balais, lesquels s'échelonnent entre 30 francs pour les balais d'essuie-glace et 550 francs l'unité pour certains démarreurs (Fiat), munis de shunts importants et ouvrageux.
Chute de tension au contact. - C'est certainement, comme nous l'avons vu à propos de la commutation, l'une des caractéristiques les plus importantes de la qualité d'un balai et en même temps la plus difficile à préciser par tout autre que celui qui a élaboré l'étude et la mise au point du prototype de la dynamo considérée et il est impossible d'en donner, dans le cas général, autre chose qu'un ordre de grandeur. Sa' valeur courante s'étale assez largement autour d'un volt et demi par balai. Elle est d'ailleurs très variable avec la pression, la température, la densité de courant, un peu avec la vitesse et surtout avec la composition du charbon. L'état des surfaces influe beaucoup, le degré de polissage et surtout l'apparition d'une patine superficielle sur le cuivre du collecteur, très favorable à sa stabilisation, qui fait qu'on peut dire de celui-ci, comme d'une bonne pipe, qu'il est "finement culotté". Ce n'est que par d'assez laborieux travaux de Iaboratoire qu'on peut en effectuer la mesure et la détermination de sa valeur optimum.
Frottement. - Lorsque deux corps solides sont appliqués l'un contre l'autre par une force F perpendiculaire à leur surface d'appui et qu'on les fait glisser l'un sur l'autre par l'effet d'une autre force f/F, tangentielle à cette même surface, on appelle "coefficient de frottement" le rapport f/F de l'effort exigé par le glissement sur la face d'appui. Dans des conditions analogues entre elles, par exemple dans le cas du frottement entre deux surfaces bien dressées, ce rapport est constant pour deux matières considérées, c'est-à-dire que la force de glissement reste proportionnelle à la pression. Pour des surfaces non lubrifiées le coefficient de frottement peut prendre des valeurs comprises entre 0,15 environ pour différents métaux et 0,70 (valeur exceptionnelle), pour le caoutchouc d'un pneumatique de voiture frottant sur le granite d'un pavé sec.
Ce sont, parmi d'autres propriétés lubrifiantes bien connues des graphites accompagnant leur conductibilité électrique qui ont fait choisir ceux-ci comme constituants de la matière des balais. Contrairement au cas des autres matériaux, le coefficient de frottement d'un balai au graphite frottant sur le cuivre d'un collecteur n'a pas une valeur constante, celle-ci variant sensiblement avec la pression, la vitesse du glissement, le passage du courant et d'une manière moins marquée, avec la température ambiante. A titre d'indication d'ordre de grandeur, un balai graphité neuf frottant sur le cuivre fraîchement avivé peut présenter un coefficient de frottement relativement élevé de 0,07 sous la pression de 200 gr par centimètre carré, qui pourra tomber vers 0,04 pour une pression moitié plus faible de 100 g/cm2. A la vitesse circonférentielle qu'il est de coutume de donner aux collecteurs, ce coefficient pourra descendre vers 0,03, valeur que le passage du courant rapprochera de 0,02. Après quelques heures de fonctionnement en charge, la suppression du courant fera remonter le coefficient de frottement d'une manière appréciable mais toutefois inférieure à celle du balai neuf par suite d'un commencement de formation de la patine.
Les coefficients de frottement ont des valeurs très variées selon la composition des balais et l'allure de leurs variations, eu fonction de la vitesse, de la pression et de la densité de courant, est aussi très variée, au point que leurs courbes, dont certaines présentent un minimum, peuvent quelquefois se croiser, une variété de balais inférieure à une autre à faible régime pouvant lui devenir nettement supérieure à un régime plus élevé.
- Quelques recommandations d'ordre pratique
Le remplacement d'un jeu de balais devrait être normalement une nécessité assez rare sur une même voiture malgré qu'elle se présente fréquemment chez le garagiste achalandé de nombreux clients. Un travail soigné doit être précédé d'un démontage de la dynamo et d'une inspection méticuleuse de ses éléments car c'est presque toujours une avarie de ses organes qui est cause d'une usure anormale. La première chose à faire est de vérifier que le balai à remplacer est bien conforme, comme marque de fabrication et numéro de référence de qualité, au type recommandé par le constructeur de la dynamo.
- Les porte-balais exigent une attention particulière
Ou devra vérifier qu'ils ne présentent aucun jeu dans leurs sertissages ni dans la fixation de leur plaque-support, ce qui aurait pour effet de permettre des variations de position des surfaces de contact avec les mêmes résultats qu'un mauvais ajustage des balais. Vérifier qu'ils n'ont pas été déformés par des manipulations maladroites, un léger bosselage ou une rugosité risquant d'empêcher le glissement du balai dans son guide ou de le rendre malaisé.
 Fig. 4. Distance h à réserver entre le collecteur C et le porte-balai P pour éviter les effets de court-circuit.
Vérifier qu'un espace d'environ 2 mm est bien réservé entre le bord métallique du guide et la surface du collecteur (voir h, fig. 4) afin que le porte-balai ne shunte pas la résistance transversale du balai.
Bien nettoyer et bien dégraisser le conduit de guidage du balai car une trace de lubrifiant suffit à fixer la poussière et à l'agglomérer en un ciment transformant à la longue le guidage de coulissement en un scellement s'opposant à l'action du ressort.
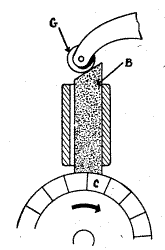 Fig. 5. Porte-balai dit "à réaction". Grâce au chanfrein arrière du balai B, le galet G du doigt de ressort applique le balai B sur la face interne du guide dans le même sens que le frottement du collecteur C..
Si le levier d'appui du ressort sur la tête du balai est muni d'un galet (fig. 5) s'assurer qu'il tourne bien librement sur son axe.
Certaines machines sont équipées de balais dont la tète est taillée en un chanfrein dont l'inclinaison est telle que la pression du galet a pour effet d'appuyer l'arrière du balai dans son guide dans le même sens que l'extrémité travaillante entraînée par le frottement du collecteur ; dans ce cas, vérifier que le chanfrein n'ait pas été, par erreur, présenté à l'envers. Mesurer la force d'appui du ressort à l'aide d'un peson ou d'un poids muni d'un crochet de fil de fer accroché à l'endroit même de portée du poussoir sur la tête du balai.
Cette force devra être égale à la valeur indiquée par le constructeur et, à défaut d'indication, jamais inférieure à 150 gr par centimètre carré de section d'appui du balai sur le collecteur de la dynamo.
Les balais de démarreurs peuvent admettre sans inconvénient des pressions beaucoup plus élevées, jusqu'à 400 gr par centimètre carré en vue d'éviter leur décollage du collecteur lors des secousses des premières explosions ; une usure ou un échauffement excessifs sous ces fortes pressions n'est pas à craindre puisque le démarreur ne fonctionne d'un très faible nombre d'heures dans la vie d'une voiture et par périodes de très courte durée.
- Le collecteur
Par son aspect, il indique souvent la source des ennuis. Un brûlage presqu'uniforme peut être causé par un graissage accidentel ou maladroitement systématique des balais ou à un défaut de porte-balai. Un brûlage étendu sur un quart de tour ou un demi-tour décèle un excentrement dû, par exemple, à un faussage de l'arbre du rotor. Le brûlage nettement localisé sur une seule ou deux lames du collecteur permet de supposer une rupture du circuit induit, souvent localisée à la soudure de la connexion de l'enroulement sur la tête de la lame du collecteur.
Le tournage du collecteur, ou sa rectification à la meule si l'on est outillé pour cela, doit être précédé d'un centrage soigné, entre pointes si les points de centres ont été respectés, sinon en mandrin, auquel cas ce centrage doit être repéré sur la partie de l'arbre correspondant à sa portée dans le palier ou dans le roulement à billes. C'est une imprudence de se centrer sur la surface du collecteur usagé qui peut avoir été tourné excentré par un dépanneur insuffisamment compétent ou usé faux-rond par l'effet combiné de la force centrifuge et d'un jeu excessif des paliers qu'il y aura lieu de remettre en état avant remontage. On arrêtera l'enlèvement des copeaux un peu avant la disparition totale du "feu" de brûlage du bord des lames puisqu'on en doit chanfreiner légèrement les bords aux interlames.
Cette opération sera effectuée, pour commencer, avec un grattoir de ferblantier après quoi on grattera le fond des micas de séparation isolante des lames à l'aide d'un grattoir spécialement taillé dans une lame de scies à métaux hors d'usage meulée selon la forme indiquée figure 6.
 Fig. 6. Profil d'un grattoir pour le grattage correct des lames de mica au fond des interlames du collecteur.
Le bec de ce grattoir sera bien rectangulaire, (vu en bout) et son angle de coupe ne devra pas être aigu mais ressembler à celui d'un outil à tourner le laiton. On retouchera alors le chanfrein à l'aide d'un petit trognon de lime carrée qu'on aura raccourcie par rupture et dont on aura meulé la cassure. Cette retouche est nécessaire pour faire disparaître les dentelures de broutage du grattoir.
 Fig. 7A. Représentation agrandie d'un interlame correctement gratté et chanfreiné. Fig. 7B. Représentation agrandie d'un interlame gratté d'une manière défectueuse. L : Lame de cuivre du collecteur. - M : Mica.
Le résultat à atteindre est représenté figure 7 A avec un fond bien propre et des bords de chanfreins bien droits. Il faut éviter soigneusement la forme de la figure 7 B qui laisse réapparaître une petite surface de mica lors de l'usure du collecteur. C'est alors seulement qu'on peut achever le tournage par une légère passe de finition avec un outil "lécheur", au fil finement avivé, ne laissant aucun filetage et qui fera disparaître toutes les barbes de chanfreinage et toutes les égratignures qu'auraient pu provoquer les outils de grattage en échappant des mains. On ne passera au polissage final qu'après avoir ajusté les balais.
- Ajustage des balais
Un balai neuf et d'origine bien calibré ne devrait pas avoir besoin d'ajustage mais il serait bon d'effectuer celui-ci au cas où le porte-balais aurait été maltraité. Le jeu à réserver sur le plat, entre le balai et son guide, doit être d'environ 2/10 de mm et, sur champ, de 3/10 de mm.
 Fig. 8. - Effet d'un jeu excessif entre le balai B et le guide P du porte-balai. Le frottement du collecteur C incline le balai qui ne porte que par des arêtes.
Un jeu trop grand permettrait au balai de s'incliner comme sur la figure 8 et de permettre des vibrations d'autant plus nuisibles que le contact ne s'effectuerait que par des arêtes et rongerait par étincelage les lignes d'appui.
S'il existe un shunt, s'assurer que son sertissage sur le balai est bien serré et que la mèche métallique est bien libre et ne risque de s'accrocher nulle part. Vérifier aussi le bon côté de la cosse du shunt qui est souvent différente selon le côté droit ou gauche de la borne de connexion.
C'est l'ajustage de la face d'appui du balai sur le collecteur qui exige les soins les plus méticuleux. Commencer le dégrossissage en creusant légèrement la face d'appui à la lime demi-ronde douce en respectant les bords d'entrée et de sortie du collecteur.

Fig. 9. - Rodage au papier de verre de la face d'appui du balai B sur le collecteur C. - MM : Bonne position du papier de verre. - NN : Mauvaise manoeuvre du papier de verre qui ne respecte pas les arêtes d'entrée et de sortie du balai
Effectuer alors un rodage au papier de verre fin en appliquant ce dernier sur le collecteur et en l'animant d'un mouvement de va-et-vient comme indiqué en MM sur la figure 9 en ayant grand soin d'éviter de déformer les arêtes de la face d'appui comme cela se produirait en tirant selon NN (même figure). Soulever le balai de temps à autre pour vérifier l'avancement du travail qui n'est terminé que lorsque toute la surface d'appui est bien rodée. Recommencer l'opération avec un papier de verre extra fin et vérifier la disparition des stries occasionnées par le papier de verre moins fin. Pendant ces opérations, bien immobiliser le balai dans son guide pour qu'il n'oscille pas lors des mouvements alternés du rodage. Si l'espace disponible ne se prête pas aux mouvements de traction selon MM, enrouler le papier de verre sur le collecteur et l'y maintenir à l'aide d'un élastique, en ayant soin de faire faire à ce papier un tour incomplet autour du collecteur pour éviter la sur-épaisseur d'un recouvrement qu'on serait tenté de laisser passer sous le balai, ce qui en défraîchirait les arêtes. Nous insistons sur la nécessité d'employer du papier de verre et non d'émeri parce que le verre possède la précieuse propriété de s'user et de s'écraser au frottement et qu'ainsi les petits grains d'abrasifs qui ont pu s'incruster dans les pores du charbon disparaissent complètement à l'usage tandis que l'émeri laisse des grains presqu'inusables (la même recommandation est valable pour les contacts percutants comme ceux des rupteurs et des relais ; lorsque ceux-ci sont usagés et présentent des cavités de corrosions, les grains d'émeri qui s'y logent peuvent inopinément en ressortir et isoler les contacts en s'y replantant, alors que les grains de verre s'écrasent aux premiers chocs).
C'est alors le moment de ressortir l'induit de la dynamo et de procéder au polissage final sur le tour, pour lequel on utilisera exclusivement des briques de pierre-ponce extra fine agglomérée que l'on peut trouver chez les fabricants de balais de charbon. Si les dimensions le permettent, on peut effectuer ce ponçage sur la dynamo toute montée. Il faut pousser cette opération jusqu'à l'obtention d'une surface glacée dans toute la zone de portée des balais.
La dernière opération, à ne pas négliger, sera un bon soufflage à l'air comprimé ou, à défaut, un brossage avec une brosse dure, mais non métallique pour éviter les rayures, et en insistant dans les interlames.
Ces multiples précautions, pourront paraître exagérément méticuleuses mais c'est seulement grâce à tous ces soins qu'on arrive à provoquer la formation de la précieuse patine en quelques heures de fonctionnement (c'est-à-dire en quelques centaines de kilomètres) et presque sans usure des balais ni du collecteur tandis qu'une insuffisance de polissage ou d'ajustage entraînerait une durée de formation de plusieurs dizaines ou même de centaines d'heures débutant par une période d'usure assez rapide et un début irrémédiable de brûlure des lames.
(Ne jamais enlever inutilement une patine bien formée, sous prétexte de présenter un collecteur bien poli).
Une dynamo traitée avec un tel soin peut conserver un fonctionnement impeccable aussi longtemps que le moteur de la voiture peut tourner sans révision. Et le client sérieux, pour longtemps satisfait de ce côté, n'hésitera pas à vous confier l'entretien de tout l'équipement électrique de sa voiture.
On peut se trouver devant une dynamo dont le collecteur est presqu'uniformément noirci, débitant irrégulièrement, s'amorçant mal (toutes connexions étant vérifiées) et dont les charbons n'ont pas besoin de remplaçants. Il s'agit souvent alors d'un brûlage par l'huile. Ne pas oublier que l'huile est le plus grand ennemi du collecteur. Il faut alors dégraisser toute la machine. Si le collecteur n'est pas abîmé, réajuster au papier de verre très fin les faces d'appui des balais et se contenter d'un repolissage du collecteur à la ponce agglomérée. Ne jamais utiliser un autre abrasif pour le polissage final.
Dernière recommandation : Lorsque les circonstances ou le temps insuffisant qu'a pu vous accorder un client ne vous auront permis qu'une remise en état partielle ou vous auront obligé à l'emploi d'un charbon incorrect, ne pas négliger d'en avertir l'utilisateur et de l'engager à compléter ce dépannage précaire à la première occasion permettant d'opérer plus posément.
|